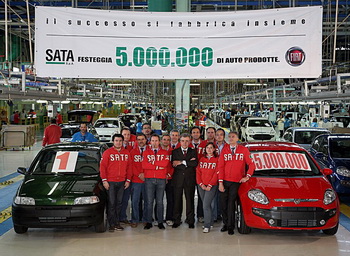 |
The five millionth vehicle has come off the
production line at Fiat’s SATA plant in San
Nicola di Melfi, Potenza, one of the world’s
most productive automotive factories; the
landmark vehicle was a Punto Evo 1.4 Emotion
in red. |
 |
|
|
|
Today the five millionth
vehicle came off the production line at Fiat Group
Automobile’s SATA plant in San Nicola di Melfi (Potenza,
Italy), one of the world’s most productive automotive
factories. The vehicle was a Punto Evo 1.4 Emotion, 105
CV, 5 doors, in red, a model which evolved from the
Grande Punto, and a car which is at the forefront of
motoring innovation, in terms of respecting the
environment, of safety and style.
The event was celebrated at the plant with a ceremony
attended by the Governor of the Basilicata region, Vito
De Filippo, the President of the Province of Potenza,
Piero Lacorazza, the President of the Confindustria
Basilicata Pasquale Carrano, the Bishop of the Diocese
of Melfi-Rapolla-Venosa, Mgr. Gianfranco Todisco and the
Director of the SATA plant, Nicola Intrevado. To
celebrate its record, the industrial site was decorated
with a series of posters on a variety of topics inspired
by the components of each of the 5,000,000 vehicles
produced, in praise of all of the plant's employees.
Retracing the main steps in the growth of the SATA plant
(Società Automobilistica Tecnologie Avanzate, Advanced
Automotive Technology Plant), where today the Punto Evo,
Grande Punto and Punto Classic models are manufactured,
allows us to understand the leading role which the Fiat
Group has played in the evolution of the organisational
structure of European factories. It all began in
September 1993, when the first Fiat Punto vehicles came
off the production line at SATA in San Nicola, 18
kilometres from Melfi. Construction of the factory
commenced two years previously.
The model immediately became a bestseller, winning
awards from the public and international critics alike
for all of its versions: from the first Punto (produced
from 1993 to 1999) to the second series (first produced
in 1999 and currently retailed as the Punto Classic),
and from the Grande Punto which came onto the market in
2005 to the latest model, the Punto Evo, which entered
the production lines in September 2009. And not
forgetting one other model which contributed
significantly to the history of the 5 million vehicles
produced in Melfi: the Lancia Ypsilon, which totalled
more than 870,000 units over its first series (1995 -
2003) and its second (2002 - 2005).
It should be noted that on 18 June 2009, the Melfi plant
was the first Italian factory to be awarded Silver Level
certification by WCM (World Class Manufacturing), an
international standard for production cycle organisation.
The WCM path to improvement includes three intermediate
stages - Bronze, Silver and Gold, before a candidate can
finally reach World Class Level. After receiving Bronze
certification in April 2007, last year SATA received its
Silver Level from the esteemed WCM Auditing Body,
presided by Prof. Hajime Yamashina. This important
recognition was achieved thanks to the widespread and
constant contribution of all personnel in applying the
WCM principles and methods, which has allowed
improvements in logistics and quality and a significant
reduction in costs.
This result is a testimony to the hard work invested
over recent years by Fiat Group to make its production
department even more efficient and flexible, a real
trump card which the company holds over even its
strongest competitors. The SATA plant is one of the
greatest examples of organisational evolution, which has
allowed Fiat Group Automobiles to grow firstly from a
traditional factory to an integrated factory (and Melfi
is one of the most important examples of factories
working with this organisational model) and finally,
through modularisation, to a modular, integrated plant.
The integrated plant is an organisational model inspired
by the principles of “lean manufacturing” (integration
of functions and tasks at all levels, decentralisation
of the decisional powers, shortening of the chain of
command and increasing of information transparency).
Modular production, which maintains all the principles
of lean manufacturing and the integrated plant, adds, on
one hand, the possibility of achieving a greater variety
and variability of products, redefining the role of the
supplier, and reduces, at the same time, complexity of
production by reducing the quantity of parts to be
assembled and simplifying operations.
|
|
|