THE CONTRIBUTION
OF OTHER FIAT GROUP COMPANIES
|
An elegant car
with a strong personality, yet one on the cutting edge in
terms of equipment, power units and mechanicals. This was
the brief given to the Alfa Romeo engineers and technicians.
To achieve it, the company deployed its best resources and
ensured that maximum quality and reliability standards were
applied throughout the product development and construction
process. It also forged profitable co-operative
relationships with its outside suppliers and some Fiat
Companies including Magneti Marelli, Centro Ricerche Fiat
and Elasis. This collaboration was responsible for many of
the innovative solutions that make the Alfa 159 the new
benchmark in its category.
Magneti Marelli
Magneti Marelli has contributed elegance, comfort,
technology and safety to the development of the Alfa 159,
the prestigious new saloon that aims to be a benchmark for
the entire segment. The exterior look of the car is
expressed to a large extent by the headlights developed by
Automotive Lighting in its plant in Venaria Reale (Turin),
which define its personality and harmonise forms and
volumes. There is a choice of two types: halogen headlights
with a 70 mm elliptical module and H7 lamp, or headlamps
with Bi-Xenon technology. The car's lights are important
design features, confirming the "family feeling" that links
the Alfa 159 and Alfa Romeo Brera.
Passenger compartment comfort is enhanced by the
infotelematic system complete with a 6.5" active matrix TFT
colour display which incorporates a satellite navigator,
radio, CD and MP3 player, hands-free GSM dual band telephone
and voice controls. The new graphics of the user interface
and a "Birdview" option for the navigator, which views the
map and the route from above, both make their debut on the
Alfa 159. And the device receives and manages RDS-TMC,
traffic news and weather forecasts through the FM radio
frequencies, displaying them as icons on the monitor.
Magneti Marelli also supplies the body computer, the
electronic control unit that manages the CAN networks and
other important functions such as diagnostics, the
immobiliser, various sensors, the lights and the fuel level.
Magneti Marelli's technological contribution to the "engine
control system" envisages the adoption of the Diesel
Throttle Module, an electronic "drive by wire" throttle
valve, on the 5-cylinder and 4-cylinder 16-valve diesel
versions, which makes it easier to turn the engine off. On
the 2.2 JTS petrol version, the Alfa 159 will adopt the
Selespeed robotised transmission: this is the latest
evolution of the fast, reliable, power-assisted gearbox
developed from Magneti Marelli's experience in Formula 1,
which first appeared on a mass production model on the Alfa
Romeo 156.
And finally, Magneti Marelli has completely redesigned the
suspension system to set a new benchmark for the balance
between handling and comfort. A high double wishbone layout
borrowed from racing experience was chosen for the front,
because it guarantees high dynamic performance, extremely
responsive steering and pinpoint driving. For the rear, the
choice went to a Multilink system which controls wheel
movement in a sophisticated manner, guaranteeing the highest
performance. The Pomigliano d'Arco and Sulmona car
manufacturing plants are involved in the industrial
panelling, mechanical engineering and assembly operations.
Centro Ricerche
Fiat
- Methodologies
The Quality
Indices (IQ), which make it possible to link the vehicle's
technical specifications to the customer's perception of
them, and therefore to design a car around the motorist that
is consistent with the brand values. In the case of the Alfa
159, for example, this means defining the qualities that
determine "uncompromisingly entertaining driving".
Setting,
deploying and achieving targets, which means starting from
assigned "customer targets" and translating them into
"technical design objectives" for the various systems on the
vehicle (suspension, brakes, steering, engine, gearbox,
etc.).
Optimisation of
the multidiscipline structure, to achieve efficient
structures for the project by maximising performance and
minimising weight. Where the Alfa 159's Premium floorpan
project is concerned, this resulted in the targeted,
effective use of multiply sheet metal, high performance
steel and laser welding.
Crash and
biomechanical methodologies, which ensure that the passenger
cells effectively protect the occupants and that the front
of the car is compatible with vulnerable subjects
(pedestrians, cyclists, etc.), respecting the demands of
current and future legislation.
Computational
fluid dynamics, which optimise external aerodynamics in
order to lower consumption and aerodynamic noise, while
respecting the car's distinctive styling, but also define
interior comfort and well-being in terms of climate and air
quality.
NVH
(Noise-Vibration-Harshness) methods, to minimise noise and
vibration creating a passenger compartment that is
comfortable and quiet in all travelling conditions, reducing
stress and enhancing well-being and alertness.
Vehicle handling
methodologies, that guarantee an enjoyable, predictable
drive in all speed, manoeuvring and grip conditions, through
painstaking design of the suspension and controls (steering,
brakes, etc.). The Alfa 159 achieves excellence in terms of
roadholding and of the steering response.Physical and
cognitive ergonomics, supported by Virtual Reality to
correctly design the interior space and systems (seat, facia,
etc.), the primary and secondary controls, the mobile parts
and the communication interfaces, which focus on the
interaction between the driver and the vehicle, at the
design stage.Bench validation methodology of the Instrument
Panel Node. This methodology generates test patterns that
comprehensively verify the correct functioning of an
instrumental panel node.
Analysis of the
virtual key: electrical/electronic architecture (definition
of the system and components) for the electrical steering
lock and "smart key".
|
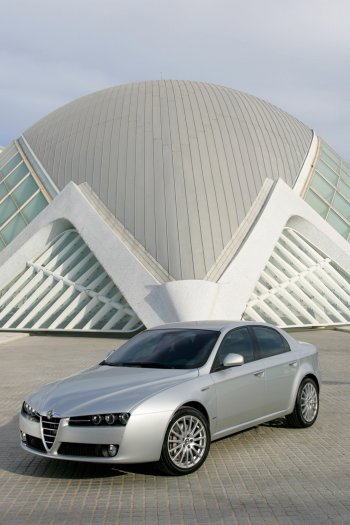 |
|
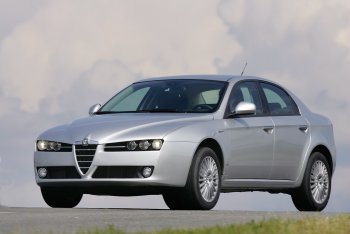
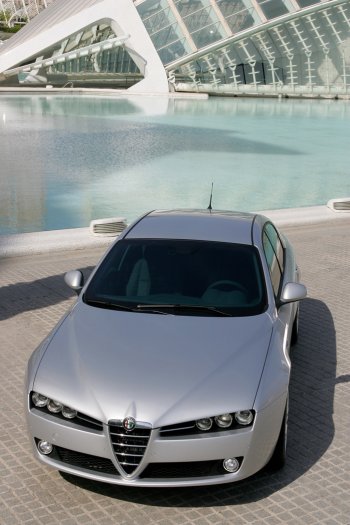
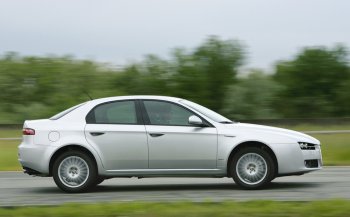 |
- Diesel engines
The basic concept of the Multijet engines and their
subsequent distinctive high performance (the 2.4 litre JTDM
delivers 200 bhp, which corresponds to more than 80 bhp/litre)
relies on innovative technologies and calculation
methodologies that have made it possible to develop and to
apply thermofluid dynamic simulation methods to the
combustion process on the JTD Multijet engines; to introduce
structural analysis of critical engine components to boost
the specific power, improve reliability and optimise
acoustic and vibrational comfort; to optimise the use of
multiple injection (Multijet) to improve performance,
emissions, consumption and acoustic comfort; and to apply
engine control strategies both to optimise performance, and
to manage the particulate abatement system by incorporating
a Diesel Particulate Filter (DPF) designed to last "for
life".
- JTS engines
The stoichiometric direct injection combustion systems
developed for the new JTS engines for the Alfa 159, were
developed by CRF. The features developed and optimised were
the definition of the inlet manifolds and the type of
injector jet that would optimise the air-petrol mix in the
combustion chamber and guarantee outstanding performance;
the definition of the piston surface geometry necessary for
the double injection that results in a 70% reduction in HC
emissions during warm-up and, if possible, allow it to
function with stratified charge idling; definition of the
compression ratio to maximise performance and reduce fuel
consumption; and definition of the mechanics and functioning
of the continuous double variable valve timing system
adopted on the inlet and the exhaust, and optimisation of
their management to enhance performance and fuel
consumption. These experiments adopted CFD fluid dynamic
analysis to design the inlet manifolds, and thermofluid
dynamics to manage the variable valve timing. In view of the
considerable increase in performance this produces, the most
crucial engine components were verified and optimised using
FEM thermo-structural and reliability analysis.
Elasis
- Control systems
Elasis was involved in the development of the electronic
control units for the new direct injection petrol engines
for the Alfa 159. Elasis developed a Hardware In the Loop (HIL)
simulator to verify that the electronic control unit
functioned correctly and the way it was incorporated on
board the vehicle well before the car went into production.
The idea behind this technology is to simulate in the
laboratory the environment in which the control units will
operate, using a real-time system. With this technology it
is possible to achieve levels of accuracy that cannot be
obtained with manual testing based on conventional systems.
What is more, during the development of these engines,
Elasis also contributed to the development of the engine
control software, concentrating in particular on all the
functions related to management of the variable valve timing
by means of "phasers". When the car went into production,
Elasis was involved in the verification and calibration of
the diagnostic systems for the engine components, focusing
its attention on components considered "Emission Relevant"
(by EOBD). Elasis also contributed to the verification of
the manufacturing process at the Pomigliano plant.
Engine-gearbox-differential, Methodologies and Technologies
Elasis performed the following activities to support
manufacture of the Alfa 159: emissions analysis on fleet
vehicles; support to the plant during the launch:
analysis/solution of specific NVH problems. Elasis also
worked on the M32 gearbox grid, being involved in its
development, by designing shafts, gears, differential,
casing and caps, performing bench tests on all the versions
for the petrol engines, and taking charge of NVH fine
tuning.
Virtual simulation of biomechanical processes in head-on
collisions helped to optimise the Alfa 159's restraint
systems, while ergonomic verification improved visibility
inside the passenger compartment. And finally, together with
the Process Engineering department of Fiat Auto
Manufacturing, Elasis developed the methodology and
industrialisation of Panelling and Assembly processes at the
Pomigliano d'Arco plant, attributing particular attention
and responsibility to the "Qualification of Manufacturing
Processes". The joint Elasis-Fiat Auto team collaborated
successfully, starting with the development of Process
Verification systems at the pilot plant of Turin-Beinasco,
and evolving machining cycles and undertaking workplace
analysis to respect process documentation developed in
simultaneous engineering by the Fiat Auto Technologies
department, in order to achieve the model process targets,
the reference gates for the "authorisation to manufacture".
|
|