The Substance of an innovative,
reliable, quality car
|
'A good product
is always a well designed product'. This was the guideline
that convinced the Fiat Bravo team to take advantage of the
best design processes to develop the new car, exploiting
virtual methodologies because they could optimise both
individual performances and their trade-off in real time.
The development of the Bravo is an excellent example of this
original approach: only 18 months separated the moment that
the product specifications were frozen from the market
launch. This is a record in the automotive world, and an
important competitive advantage, since being able to develop
a car rapidly means responding better to market demands. But
to be not only fast, but rigorous and excellent too,
requires cutting-edge technology and extremely precise
engineering processes. This rigour has been applied at all
stages of the development and industrialisation of the
Bravo, applying the most advanced, innovative reliability
methodologies. It was a winning project, which had three
specific objectives: outstanding safety, enjoyable driving
and the best quality of life on board.
Engineering excellence that
goes a long way back
To build a revolutionary engine, innovative systems and cars
that are a success overall, a manufacturer must employ
cutting-edge technologies and methodologies that interpret
the customers’ wishes, to achieve a level of comfort and
performance that set them apart from the competition, low
consumption and emissions in all conditions, and the highest
levels of safety, quality and reliability. Ambitious goals
that have always placed the Fiat Group among the pioneers in
the application of virtual analysis to design. Even in the
1970s, the structural components of a vehicle were verified
by computerised calculation techniques, and early in the
1990s, the company acquired one of the first
'super-calculators' for commercial uses (the famous Cray
supercomputer), only the third in Italy, when there were
very few in Europe, generally used for scientific
calculations in universities or large research centres. And
the company has always kept up with the latest virtual
technologies on the market, in many cases actually
anticipating them thanks to the work of its own Research
Centres.
The Fiat Bravo is the
outcome of a winning development process
At Fiat Auto, the development process starts from stringent
objectification of performance, as seen by the customer
first and foremost. This allows all objectives to be
measured, so that the development process can be organised
in three main stages: target setting, target deployment and
target achieving. It is the latter that has been
revolutionised by the introduction of virtual verification
cycles, which drastically cut development times and costs,
increasing the team’s confidence in the possibility of
achieving its initial goals. Research in the field of
simulation has focused on the creation of mathematical
models that can provide an increasingly exact estimate of
the physical parameters that are most representative of a
vehicle’s performance.
We should point out that there has not only been an
evolution in physical simulation calculations. Take the huge
graphic potential of the new IT tools, which make it
possible to visualise physical objects with the utmost
realism. From the evaluation of the styling to verification
of layouts and access to components, virtualisation of the
assembly line and immersive verification of physical and
cognitive ergonomics: all the systems on the vehicle and the
plant necessary to produce it can be 'seen' by specialists
exactly as they are in reality, immediately after they have
been drawn by the designer.
That is not all. The development process is backed up by
powerful planning, checking, technical data filing and
monitoring systems. The integration and close connection
between the system that established a single BoM for
engineering and manufacturing, known as CAD/CAE PDM, the
archive of standards and the unified system of product
objectives and the authorisations, both physical and
virtual, that constitute a 'backbone' for the management of
information that is practically unique in the automotive
world. These systems are constantly updated in real time and
available both to suppliers and, obviously, to all the Fiat
Auto design centres all over the world.
But we must not forget that to achieve a quality product
like the Fiat Bravo, state-of-the-art CAE methodologies must
be adopted at all stages of its development. To do this, the
company has relied on the collaboration of its best
suppliers, and has created its own model which programmes
all the stages organically: from the initial scenario,
through the strategic configuration, innovation,
standardisation and analysis of the initiative, right down
to final technical and technological development, the
integration of suppliers, final quality verification and
manufacturing build-up.
From styling to 'perceived
quality': how the entire process is organised
As soon as the styling starts to take on a possible
configuration, the feasibility of the individual parts is
verified virtually, and the aerodynamic behaviour of the
shapes of the vehicle are assessed; then preliminary
ergonomic checks are performed on the first styling
proposals. In the meantime, the styling and the virtual
checks consolidate the choice of the definitive model,
triggering the real design process. The skeleton takes
shape, and work can begin on the shape of the bodyshell.
Today, Fiat Auto’s CAD designers are in a position, when
necessary, to perform the first static verification on the
most crucial CAD parts using calculation tools that are
totally incorporated into their CAD environment, simply and
rapidly. The most detailed, complex calculations are
performed by specialists, but even their work has been
simplified, because they have direct access to CAD
mathematical calculations through the company database which
includes the drawings of all our models.
The DMU, the digital mock-up of the assembly of all vehicle
components, is integrated into the database, which makes it
possible to verify their layout, ease of assembly and access
for service, even using totally immersive virtual reality
techniques. As soon as the 'body in white' has been
completed designers receive immediate feedback from the
ergonomists, who verify the visibility zones and reflections
by calculation, to correct the design of the space, the
interior systems (seats, facia, etc.), the primary and
secondary controls, the mobile parts and the communications
interfaces. At the same time, the first vehicle dynamic
calculations begin, as does verification of the mechanical
components. Specific simulation models have been developed
in the field of Handling and Ride Comfort, that include all
the controlled active systems that are present today, from
ABS to stability control.
The bearing structure of the early stages of technical
development is based on milestones of the CAD drawings
present in the database. The virtual structural verification
of the safety, rigidity and fatigue resistance aspects gets
underway from a very clear level of maturity. In the safety
field, Fiat Auto applies the latest methodologies to
simulate the effects of impact on the structure, on the
human body and on pedestrians, including simulation of the
activation and control of the active restraint systems.
These include crash and biomechanical methodologies, to
ensure that the passenger compartment cell protects
occupants and that the front of the vehicle is compatible
with vulnerable subjects (pedestrians, cyclists, etc.),
respecting current and future legislation. This means that
it is possible to verify the objectives set by the initial
project much earlier using virtual methods than would be
possible with real simulation, using prototypes.
All the other performance parameters are approached in a
similar manner: fatigue, acoustics, climate, performance and
consumption. For example, CAE methodologies have been
applied throughout the development of the chassis, with
particular reference to the performance targets for both
fatigue resistance and NVH (Noise-Vibration-Harshness)
quality. First of all, the fatigue resistance of the chassis
was developed and approved by calculation, using FEM methods
to virtually simulate typical missions that generate
fatigue, a system already in use for bench testing. Good
consistency has been achieved between the calculation and
the experimentation, thanks above all to the integration of
multi-body calculation methodologies (dynamic simulation of
the vehicle during its mission) and FEM calculation
methodologies (structural calculation of stress and fatigue
damage).
Even the smallest details linked to quality are carefully
analysed and calculated. Design of Experiments techniques
are used to explore all the possible cases related to
manufacturing variables (geometries, material
characteristics, coupling, etc.) in order to ascertain that
there is no anomalous behaviour (bangs, squeaks, creaks,
etc). Virtual approval activities related to steering-wheel
vibration (crossbeam and column), engine noise (structural
measures at the anchorage points) and advancement noise
(suspension blocks and bushes) are all part of this process.
The end result of the entire development process is the Fiat
Bravo, a top quality car that is absolutely innovative,
created in record time, and the fruit of expertise that is
unique in the automotive world.
A project that refutes two
myths regarding virtual verification
Until now, it was widely thought that virtual verification
could not completely replace the tests on physical
prototypes used to reach the final approval of a project. At
most, people recognised that virtual verification eliminated
a few experimental cycles on the first mock-ups, which were
known to be of little significance, and that they could be
useful during fine-tuning and problem solving. Which is why,
even with significant disadvantages (slowness, high costs,
need for test tracks and laboratories), physical prototypes
continue to be used, even when they were obsolete with
respect to the stage of development of the project. This was
certainly the case at Fiat. Until the Bravo. But now a new
approach to design was needed, to cut time and costs, while
respecting the demands of an innovative, top quality project
like that of the Bravo. So, taking into consideration the
increase in hardware performance which has stimulated the
growth of increasingly sophisticated calculation
applications, the team used the latest resources in this
field, drawing on the expertise gained in this field by Fiat
Auto in years of experience, also verified outside the
automotive field. The Bravo was the first car to be
developed adopting exclusively virtual verification systems.
Another myth was that virtual verification could at most
replace the corresponding physical experiments; in actual
fact there is more to it than that. Virtualisation of the
vehicle creates a practically infinite number of prototypes
which can be subjected to a practically unlimited number of
tests. This also makes it possible to apply the most
advanced statistical methodologies in the field of
optimisation and 'robust design'. It means that Fiat Bravo
has been subjected, virtually, to many more tests than would
have been possible using traditional methods and physical
prototypes; plus the fact that with these tests it is
possible to measure a quantity of information that cannot
normally be managed by classic experimental measurements. In
practice, the construction of the mathematical models and
their interactive use, allows the Fiat Auto engineers to
acquire much more detailed understanding of the vehicle than
in the past, and to explore its behaviour in the tiniest
detail. The project is therefore 'optimised' (i.e. with
greater quality, obtained with less trouble and cost) as
well as 'robust' (the end product will be more insensitive
to the inevitable manufacturing deviance and changes over
the years of its use by the customer).
Class-beating safety
Fifteen thousand hours of calculation, 60 crash tests, one
hundred and fifty simulation cycles with a HyGe sled, and
one hundred tests on components and subsystems. These
figures underline the company’s commitment to making the
Bravo one of the safest cars around, not only in its segment
but on the entire car market, because the model is
state-of-the-art where passive safety systems are concerned.
Total protection, in other words, which starts with the
devices that are dedicated specifically to safety: as many
as 7 airbags, three-point seat-belts with pre-tensioners and
load limiters, five head-restraints and the FPS fire
prevention device. Then the new chassis, which was designed
to absorb any impact very effectively. And finally, the
contribution made to the protection of occupants by the
bodywork, the bonnet, doors and facia crossbeam. Nor can we
overlook the contribution made to passive safety by other
elements such as the seats or the steering column, which
were designed taking their behaviour in an accident into
consideration.
The Air-Bag Smart 2 system
Complete protection, intelligent protection. In a head-on
impact, occupants are protected by an innovative restraint
system known as 'Air-Bag Smart 2', because it automatically
adapts the activation parameters to the severity of the
accident. Starting from the driver’s front airbag, which
adopts a different logic from conventional airbags. Until
now, when the airbags were activated, they inflated
simultaneously up to their maximum limit, which was
established to safeguard occupants during severe impacts.
The Fiat Bravo, on the other hand, adopts a driver’s front
airbag with dual-stage activation; this means that the
system only activates the first of the two stages when the
impact is of moderate strength, but activates both in the
event of a more serious collision. The two stages can also
be activated with different sequences depending on the type
of impact. In any case, the bridles inside the bags
guarantee that the maximum dimensions and the shape taken by
the cushions are as non-invasive as possible for passengers.
The front passenger airbag can obviously be de-activated
(using the menu on the control panel), to carry a child in a
safety seat facing backwards on the front seat (the pre-tensioner
on the other hand remains active).
The sensors of the 'Air-Bag Smart 2' system also control the
activation of the seat-belt pre-tensioners. The Bravo is
fitted with front seat-belts that are each complete with an
inertia reel, pre-tensioner and load limiter. On impact, the
electronically controlled pyrotechnic pre-tensioner retracts
the belt in a few milliseconds, so that it adheres perfectly
to the body. The load limiters are positioned inside the
inertia reels, and they yield in a controlled manner,
metering the force exercised by the belt on the shoulder of
the person wearing it. And finally, the front protection
system of the Bravo offers the option of an airbag under the
steering column, to render this area, traditionally the most
dangerous for the knees, inoffensive.
The control unit and the
sensors
The Fiat Bravo is fitted with all the most advanced passive
safety devices available today. A sophisticated 'nervous
system' has been developed to manage them, governed by an
electronic control unit in the front tunnel. This system
receives the signals from the various sensors positioned
around the car (in addition to those inside the system
itself), and on the basis of these signals decides how many
and which devices to activate. This is why the system
behaves in an 'intelligent' manner. It is not activated
when, in spite of an impact, there is no danger that an
occupant will collide with the surfaces of the car. It
recognises stress that does not derive from a collision, and
continues to function even if there is an electrical
blackout. This is all made possible by particularly
sophisticated functioning logics and detection terminals.
Such as the CSA (Crash Severity Algorithm), which recognises
the severity of an impact and controls the front airbags, or
the sensor that detects the presence of a passenger, and can
warn the occupant to fasten his seat-belt, by a beeper or a
telltale on the instrument panel. Or the ECS (Early Crash
Sensor), the decentralised sensor that measures head-on
impact, an additional device positioned in the front of the
car, that enables the control unit to anticipate the
activation of the front airbags; this allows the airbag to
be completely inflated before the occupant has even begun to
move forward towards the steering wheel or facia, unlike a
conventional system.
Curtain-bags and sidebags
The former are airbags that descend down the windows to
protect occupants’ heads in the event of a side-on
collision. The curtain-bags adopted on the Bravo are more
protective than other systems (because they always take up
the correct position), faster to inflate and less invasive
for passengers. They open from the top down and there is no
risk of their causing secondary injury to the occupants’
arms with their movement. They also effectively protect the
heads of both front and rear passengers, because they extend
the whole length of the side windows, protecting occupants
even if the car overturns. The two bags (one on each side)
are positioned under the longitudinals of the roof, folded
inside a closed compartment. At the appropriate moment, the
cover bends to allow the bags to inflate and to descend.
And finally, to protect the pelvis and chest of passengers
even if they hit the sides of the car, the Fiat Bravo also
fits sidebags inside the seat squabs, where they protect the
occupants best, regardless of the latter’s stature or
position, or how the seat is regulated.
More stringent tests for
total protection
The experts at the Fiat Safety Centre at Orbassano (outside
Turin) subjected the Fiat Bravo to all possible types of
high speed collisions in order to verify the effectiveness
of the integrated protection system developed for the new
model on the spot. They then analysed the results on the
basis of the structural and biomechanical parameters
envisaged by some of the world’s most stringent legislation.
The following results were obtained.
Head-on impact
The Fiat Bravo achieved excellent results in two different
types of tests. The first was performed at a speed of 64
km/h against a deforming barrier which simulates a head-on
impact between two cars; the second envisages a crash at 56
km/h against a fixed, rigid barrier. Thanks to the robust
structural architecture and the use of highly
energy-absorbing materials, the intrusion levels measured on
the Bravo during these tests were very low and allowed all
the doors to open, without generating significant inertia
stress on occupants, because this was efficiently absorbed
by the Smart Air-Bag system. And finally, in the case of
head-on impact, the items carried in the Bravo’s luggage
compartment do not hit passengers.
Side-on impact
Two tests recognised internationally bear witness to the new
model’s ability to guarantee the safety of front and rear
passengers, even in the event of a high speed side-on
collision. The first is 'Impact against a deforming
barrier'; the Bravo reacts superbly to this test, which
simulates a collision at 50 km/h between two vehicles at a
90° angle, thanks to the protection offered to the pelvic
area by the robust bodyshell structure, to the abdomen and
chest by the combined action of the sidebags and door
panels, and to the head by the curtain-bags. The second test
is 'Side-on impact against a pole', one of the most
dangerous for motorists.
Rear impact
During rear
impact tests, attention is focused, in structural terms, on
containing the deformation of the passenger compartment and
on preventing any damage to the fuel tank, which could cause
a fire. What is more, from a bio-mechanical viewpoint,
efforts are concentrated on guaranteeing that the seats
support the occupant well without collapsing, and on
minimising any injury, particularly to the neck and head,
which are usually the most vulnerable parts of the body.
Protection of pedestrians
The styling of the front part of the Fiat Bravo was
developed bearing the protection of pedestrians in mind. The
volumes are smooth and rounded, and there are no sharp edges
that could injure pedestrians. The large surface of the
bonnet minimises the risk that a pedestrian’s could hit the
front uprights. The sturdiest components in the engine bay
are positioned at a suitable distance from the bonnet, to
allow the 'skin' of the bonnet to absorb the energy deriving
from impact with a pedestrian’s head.
Protection of children
The new model also features all the devices that guarantee
absolute safety for children travelling in the car. The most
important, and most effective, of these are the Isofix
attachments on the rear seats, and the de-activation of the
front passenger airbag by the onboard computer.
Protection against fire
From the bodyshell down to the smallest component, the Fiat
Bravo was designed and built to meet Fiat’s latest, and
strictest, internal fire prevention standards. For example,
the Fire Prevention System which instantly cuts off the
electric pump on petrol-engined cars and the fuel supply
solenoid on diesel models, in the event of serious impacts.
The switch is positioned under the lining of the right front
door pillar, while the plastic fuel tank, which already
meets future legislative requirements, is positioned where
it is protected in a collision, and built to resist
deformation with no loss of fuel.
Active safety
The Fiat Bravo adopts the most sophisticated electronic
systems to control the vehicle’s dynamic behaviour, which
are implemented to raise the dynamic limits even higher, so
that they enhance safety but are not intrusive for the
driver. The intervention of these devices is the result of
simulation and specific tests on the test track, to ensure
that they do not detract from the pleasure of driving. A
description of the lavish equipment follows.
Braking system and large
tyres
In line with its high active safety targets, the Fiat Bravo
is equipped with extremely efficient, highly adaptable
braking systems. To start with, the braking system is
hydraulic, with servo assist, and features 2 cross-over
independent circuits (each circuit acts on one front wheel
and the opposite rear wheel) to guarantee braking and
stability even if one circuit should fail. All the versions
in the range are fitted with ventilated disc brakes at the
front, and with solid discs on the rear wheels, which vary
with the engine, to reflect the different weight and power.
For example, for the 1.4 16 valve engine, ventilated discs
with a diameter of 257 x 22 mm are fitted, and rear discs
with a diameter of 251 x 10 mm. The version powered by the
120 bhp 1.9 Multijet adopts 284 x 22 mm ventilated discs and
solid discs of 251 x 10 mm. And finally, the 150 bhp 1.9
Multijet engine fits 281 x 26 mm ventilated discs and solid
discs of 251 x 10 mm. To achieve the best compromise between
handling and comfort, the Fiat Bravo fits large tyres that
optimise the car’s performance, particularly in terms of
roadholding, safety and comfort on the road. The tyres
chosen (depending on the outfit) are: 205/55 R16, 225/45 R17
and 225/40 R18.
ABS complete with EBD
(Electronic Brake force Distribution)
In addition to its excellent braking system, the Bravo is
also equipped with one of the most advanced ABS anti-lock
braking systems on the market. It includes a hydraulic
control unit with 8 solenoids, 4 active sensors and 4
channels with EBD electronic brake force distribution. The
latter distributes the braking force over the four wheels to
prevent them from locking, guaranteeing complete control of
the car in all conditions. The system also adapts
automatically to the grip conditions of the wheels and the
efficiency of the brake pads, preventing the latter from
overheating.
ESP (Electronic Stability
Program)
The sophisticated ESP system cuts in when conditions are
close to the limit, when the car’s stability is at risk, to
help the driver to control the vehicle. To do so, ESP
constantly verifies how the tyres grip the ground,
longitudinally and laterally, and if the car does skid, it
cuts in to recover the trajectory and the stability of the
set-up. It incorporates sensors that measure the vehicle’s
rotation around its vertical axis (yaw speed), the lateral
acceleration and the steering angle set by the driver (which
indicates his chosen direction). It then compares these data
with the parameters processed by a computer and uses a
complex mathematical model to establish whether the car is
taking a bend within grip limits, or whether the front or
rear are about to veer (understeer or oversteer). To bring
it back to the correct trajectory, the system generates a
yaw moment opposite to the one that caused the instability,
singly braking the appropriate wheel (nearside or offside),
and reducing engine power by adjusting the throttle valve.
This is where the system developed for the Fiat Bravo
differs from other systems. Its intervention on the brakes
is modulated to be as gentle as possible (therefore without
disturbing driving), and the reduction in engine power is
limited, to guarantee excellent performance and enjoyable
driving at all times. ESP is always engaged.
Hill Holder - HBA
The Hill Holder, which is an integral part of the ESP
system, helps the driver during hill starts. It cuts in when
the ESP control unit perceives a difference in the
inclination of the car through a longitudinal acceleration
sensor. During a hill start, the control unit prepares to
cut in when first speed is engaged and the brake and clutch
pedals are depressed. The pressure on the front brake
callipers is maintained for about 1.5 seconds after the
driver removes his foot from the brake pedal, allowing him
to set off without difficulty. The Hill Holder is not
activated when the car is started downhill in first gear.
The same occurs when reverse is engaged: the system is
activated for downhill starts, and it is not activated for
uphill starts. And finally, there is the option of HBA,
electro-hydraulic brake assistance, which automatically
increases the pressure on the braking circuit during panic
braking.
ASR (Anti Slip Regulation)
Another integral element of the ESP system is the ASR (Anti
Slip Regulation) system, which optimises traction at all
speeds, using the brakes and engine management. Based on the
number of wheel revs calculated by the ABS sensors, the
device calculates the degree of slipping and activates two
different control systems to recover grip. When an excessive
demand for power causes both drive wheels to slip (for
example when aquaplaning or accelerating on an uneven,
snow-covered or icy road surface), the system reduces engine
torque by decreasing the throttle valve aperture and thus
the air flow. If only one wheel slips (for example the wheel
inside a bend following acceleration or dynamic changes to
the load), this is automatically braked without the driver
having to press the brake pedal. This obtains an effect
similar to that of a self-locking differential, enabling the
Bravo to tackle road surfaces with poor grip without
difficulty.
ASR is engaged automatically every time the engine is
started, but can be excluded by a switch on the centre
console. It is only necessary to de-activate ASR when
fitting snow chains, because in order to transmit torque to
the ground, the wheel has to be able to 'pile up' snow with
small slips that the ASR system tends to avoid.
MSR (Motor Schleppmoment
Regelung)
This device, also an integral part of the ASR system, cuts
in when there is a sudden change of gear when changing down,
to return torque to the engine and prevent excessive
dragging of the drive wheels, which could cause the car to
lose stability when grip is poor.
Engines and gearboxes:
extremely enjoyable to drive
Behind its distinctive styling, the Fiat Bravo offers a
comprehensive range of excellent engines that feature
state-of-the-art engineering and generous performance. The
range comprises two Multijet turbodiesel engines (1.9 8v
delivering 120 and 1.9 16v delivering 150 bhp) and three
petrol engines: a 90 bhp 1.4 16v, and two 1.4 16v
turbocharged engines from the new T-JET family, delivering
120 and 150 bhp (which will be available after the launch).
Each engine offers different advantages, all of which are
exploited in full by being combined with 5 or 6-speed
gearboxes, and they stand out for their generosity, their
sparkling temperament or their outstanding performance and
sophisticated technology. But all the engines are extremely
reliable and environment-friendly.
All the engines mounted on the Bravo are manufactured by
Fiat Powertrain Technologies, the Group’s new sector. FPT
draws together all the activities in the fields of
innovation, research, design and manufacture related to
engines and gearboxes for all types of applications: from
cars to commercial vehicles, boats and agricultural
machinery. With approximately 19,000 employees, 17 plants
and 10 research centres in eight different countries, the
Sector is one of the world’s most important organisations in
its field. At FPT, approximately 3000 highly specialised
technicians focus on the development and engineering of
innovative technologies. More than 40 patents are filed each
year, confirming the quality and seriousness of this
commitment, and making Fiat a huge center of technological
excellence and constant innovation.
Powerful, smooth engines
The new T-JET family
A new family of turbocharged petrol engines, known as the
T-JET, will make its debut on the Bravo soon after the
launch, featuring outstanding performance, prompt response
to the accelerator, low consumption, constructional
simplicity, sturdiness and reliability. The new 1.4 16v
turbo engine will be available in two versions: the first is
more sporty, delivering a maximum of 110 kW (150 bhp) at
5500 rpm, while the second is more of a 'tourer', and
delivers 90 kW (120 bhp) at 5000 rpm. Both offer a peak
torque of 206 Nm (at 2000 rpm on the 110 kW, and at 1750 rpm
on the 90 kW), but 230 Nm (at 3000 rpm on the 110 kW) is
available, simply by pressing a key on the facia (the SPORT
150 bhp version). The engine is very elastic, requiring
fewer gear changes, for an enjoyable, relaxed driving style,
but it will respond assertively if the driver puts his foot
down. This is one effect of the low inertia of the
turboblower, which makes it possible to obtain top
performance by acting on the accelerator, with none of the
annoying delays typical of this type of engine. The result
is outstanding sportiness combined with fuel economy.
The outstanding reliability of the engines is guaranteed by
the hundreds of thousands of kilometres driven by prototypes
during the development stage, in addition to thousands of
hours of static and dynamic tests on the bench. The first
maintenance is programmed after 30,000 km, and there is no
need for any intermediate servicing. The oil/water heat
exchange guarantees these results. The oil filter is of the
environment-friendly type.
The computerised engine control system manages all functions
using sophisticated calculation algorithms. The accelerator
control is of the 'drive-by-wire' type, without mechanical
connections, so that the driver can obtain the relaxed or
sporty response he wants from the engine, without wasting
energy.
These excellent results have been obtained by painstaking
design and development of all the engine components,
demanding over 120,000 hours of activity. State-of-the-art
computer-assisted design and calculation systems were used,
making it possible to simulate the greatest stress caused by
the turboblower. All the major components have been
re-designed, so that we could describe the engine as
completely new. Particular attention was paid to fluid
dynamics and combustion, to minimise energy losses and to
obtain top performance and low consumption, and the results
were guaranteed by sophisticated experimental analysis.
The 90 bhp Fire 1.4 16v
engine
This engine is a member of the Fire family, and it has a
capacity of 1368 cc, and 4 cylinders in line with a bore of
72 mm and stroke of 84 mm. There are four valves per
cylinder, activated directly by 2 overhead camshafts. The
engine was developed paying particular attention to
performance and to fuel economy, two areas in which the Fiat
Bravo leads its class. The merit goes to the volumetric
efficiency which has been optimised all through the
operating range, thanks to a specific fluid-dynamic
development of the entire intake system and the timing. The
engine delivers 90 bhp (66 kW at 5500 rpm) and peak torque
of 128 Nm (13 kgm at 4500 rpm). With this engine, the Bravo
has a top speed of 179 km/h, and accelerates from 0 to 100
km/h in 12.5 seconds. Sparkling performance, in spite of low
consumption: 8.7 l/100 km in the urban cycle, 5.6 l/100 km
out of town and 6.7 l/100 km in the combined cycle.
A sparkling engine that is sparing on fuel. This has been
achieved thanks to the adoption of a throttle valve control
system known as 'drive by wire'. The 90 bhp 1.4 engine also
adopts a new, 'torque-based' engine control unit, which is
the state of the art in this field. Its most interesting
feature is that it activates all devices through a single
coordinator block, whose basic parameter is the torque
demanded by the driver when he puts his foot on the
accelerator. Translated into a physical torque value, the
various demands (including those of the external systems
such as ABS) can be coordinated even before the main engine
control parameters have been converted (advance, throttle
valve position, injection time, etc.) with the enormous
advantage of being able to generate them with great
precision and in a very short time. This system exploits a
single communications standard between the various systems
and functions, whose common 'language' is the engine torque.
This makes for a level of driveability superior to that
available from current systems, while also reducing
polluting emissions.
Other features peculiar to the new 90 bhp 1.4 16v Fire are
the optimisation of the compression ratio and the high
torque values at low speeds, characteristics that make it
possible to limit fuel consumption. This target has also
been reached thanks to the calibration of the latest
generation engine control unit, which keeps fuel consumption
very low, compatible with the requirements of driveability,
performance and emissions. A catalytic converter positioned
in the engine bay (and welded to the exhaust manifold flange
using a new technology) reaches very high temperatures very
fast, thus reducing emissions even while the engine is
warming up. To minimise the environmental impact, the engine
also incorporates a returnless fuel supply system, which
eliminates fuel recirculation within the tank, thus reducing
vapour formation. High performance, sparing on fuel and
clean: to these winning features the 90 bhp 1.4 16v Fire
engine also adds excellent acoustic comfort.
The 120 bhp and 150 bhp 1.9
Multijet
Both have 4 cylinders in line, with two valves per cylinder
and four valves per cylinder respectively, a bore of 82 mm
and stroke of 90.4 mm; the first delivers 120 bhp (88 kW) at
4000 rpm and torque of 255 Nm at 2000 rpm, while the second
delivers 150 bhp (110 kW) at 4000 rpm and torque of 305 Nm
at 2000 rpm. Several changes have been made to the
engineering of the two engines to boost performance and
engine torque at low speeds, and to reduce noise and
vibration. For example, the 'Common Rail' system envisages
two strategies for automatic control of the calibration and
balancing of the injected diesel fuel, improving acoustic
and vibrational comfort.
Turbocharging is entrusted to a Garrett VGT 17 turbo, with
electronic management of the variable geometry, which
improves power delivery while guaranteeing very high torque
values even at low engine speeds. For example, 90% of peak
torque is available between 1750 and 3250 rpm. This
translates into extremely enjoyable driving and excellent
performance. The Fiat Bravo equipped with the 120 bhp 1.9
Multijet engine has a top speed of 194 km/h and accelerates
from 0 to 100 km/h in 10.5 seconds (with the 150 bhp 1.9
Multijet the top speed is 209 km/h, and 0-100 km/h
acceleration takes 9 seconds). Brilliant performance in
other words, but fuel consumption remains low: 6.9 l/100 km
in the urban cycle, 4.3 l/100 km out of town and 5.3 l/100
km in the combined cycle for the 120 bhp Multijet, while the
150 bhp version returns 7.6 l/100 km for the urban cycle,
4.5 l/100 km out of town and 5.6 l/100 km in the mixed
cycle. We should also underline that the 120 bhp 1.9
Multijet achieves an excellent 139 g/km where emissions are
concerned.
The second generation turbodiesel engines are still based on
the principles of the 'Common Rail'; i.e. high injection
pressure and electronic injector control. But the new
generation engines have an additional feature: during each
engine cycle, the number of injections has been increased
from the two that are common today. The same amount of
diesel fuel is burned inside the cylinder, but it is burned
in portions, producing smoother combustion. The advantages
include quieter operation, lower emissions and a 6-7% boost
in performance accompanied by engine efficiency that makes
the car even easier to drive.
These results are significant, because they have been
achieved on an engine which represents an incredible leap
forward compared to pre-combustion diesels, and even
improves on first generation JTDs. The secret of the
Multijet lies both in the control unit that governs the
electric injector opening and closing system and the
injectors themselves. The crucial element is the electronic
control unit itself, which performs a series of extremely
close injections. The components (and the injectors) were
developed by Fiat’s researchers to do just that; it delivers
the multiple injections that guarantee more precise control
of the pressures and temperatures generated in the
combustion chamber, as well as exploiting the air taken into
the cylinders more efficiently. This achieves other goals:
lower combustion noise, reduced emissions and boosted
performance.
|
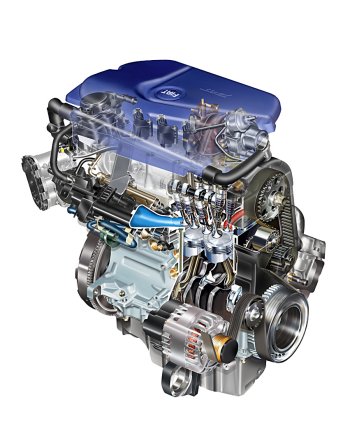 |
Fiat Bravo - 1.4 16v
T-JET |
 |
|
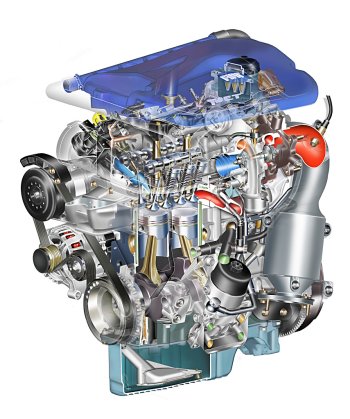 |
Fiat Bravo - 1.4 16v
T-JET |
 |
|
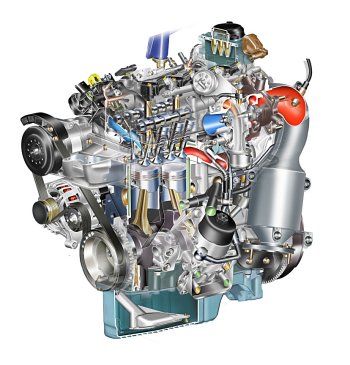 |
Fiat Bravo - 1.4 16v
T-JET |
 |
|
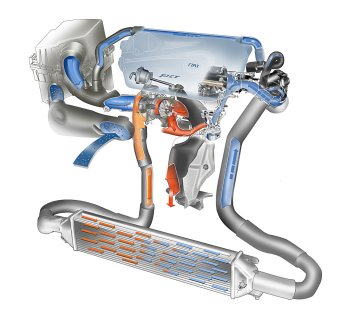 |
Fiat Bravo - 1.4 16v
T-JET |
 |
|
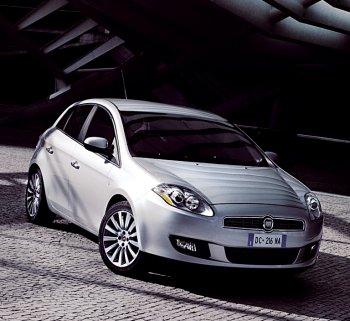 |
|
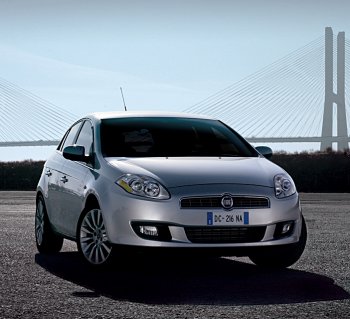 |
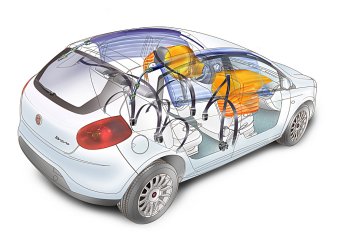 |
Fifteen thousand hours of calculation, 60 crash
tests, one hundred and fifty simulation cycles with
a HyGe sled, and one hundred tests on components and
subsystems. These figures underline the company’s
commitment to making the Bravo one of the safest
cars around, not only in its segment but on the
entire car market, because the model is
state-of-the-art where passive safety systems are
concerned. |
 |
|
The development of the Multijet system is the outcome of
years of research. Initially, the technicians solved the
problem of the limits posed by the control units. They then
drew a map of the benefits obtained by plotting different
multiple injection sequences (two secondary injections very
close to the main injection, one secondary not too close to
the main injection plus two other close secondaries; one
secondary, followed, at a certain interval, by two
closely-spaced main injections, etc.) with the various
operating ranges of the engine: idling, with low loads and
low rev speed; with high revs and a moderate load; with low
revs and a high load, and so on.
This analysis revealed the potential of the system, and
showed that great benefits are achievable at all times,
though they tend to focus on one field or another, depending
on the type of sequence chosen and the engine service range
targeted. In some cases, the priority is to reduce starting
times and fume levels, in others, it is to increase torque
and reduce noise, in others still, it is to reduce emissions
and noise levels. Today this research has resulted in the
development of the Multijet engines.
The two Multijet units are friendly to the environment,
incorporating an electronic EGR system which cools the
recirculating exhaust gases, and a 'close-coupled' catalytic
converter, as well as a particulate trap (DPF), a 'for life'
system that abates fine dust and is regenerated without
additives. In other words, a long list of improvements and
measures to produce a reliable, powerful engine that is
sparing on fuel.
All the versions have the hydraulic coaxial clutch release
mechanism (CSC) developed for the 1.9 Multijet engine. This
device, which does not have external actuators, guarantees
greater efficiency of the system during the life of the car
and also makes it possible to isolate the noise and
vibration produced by the engine. Unlike a hose control,
this hydraulic system provides for self-regulation of the
worn pedal. The system is also combined with a device that
recovers friction plate wear, which maintains the load of
the clutch pedal constant throughout the life of the
vehicle. The optimisation of the components and the use of
innovative materials (plastic, aluminium) has made it
possible to reduce the weight by more than 2 kg compared to
a conventional hydraulic control.
And last but not least, in line with European directives to
protect the environment, only environment-friendly friction
materials have been used on all versions, whether petrol or
diesel. Finally, the friction pump body is made of plastic,
which also reduces the weight, with a steel cylinder and a
plastic piston. The material for the piston and the rubber
sealing rings have been developed specifically to operate
with long strokes, while the seal created by the contact
between rubber and steel is a great improvement on
conventional friction pumps which have a cast iron sealing
surface.
Reliable, sophisticated
gearboxes
An innovative model like the Fiat Bravo had to be on the
cutting edge where gearboxes are concerned, because this
component has a decisive influence on driving enjoyment and
comfort. The new car offers a choice of two, with two
specific variants depending on the engine.
These are the available combinations:
- with 6 speeds on the 90 bhp petrol-driven 1.4 16v (C514);
- with 5 speeds on the 1.9 Multijet 8v (C530);
- with 6 speeds on the 1.9 Multijet 16v (C530).
All the gearboxes share the same dual hose external drive,
which guarantees precise manoeuvring, quiet operation and
does not transmits mechanical vibration through the control.
This is a new generation external control, technologically
advanced thanks to the extensive adoption of high
performance technopolymers, which are used on the basis of
different characteristics of resistance, weight and
self-lubricating power.
Bench testing in extreme climate conditions guided the
fine-tuning of the materials, couplings and processes, and
guarantees the 'robustness' and reliability of the product.
In addition to which, the new drive was designed to
guarantee system characteristics, excellent comfort and
manoeuvring. A new distribution of the inertia masses was
adopted, significantly closer to the gearbox, to raise the
level of comfort by increased mechanical filtering. And huge
attention is paid during the assembly of these components to
guarantee their quality and reliability, with pre-testing of
every component and electronic measurement of all the values
that define efficiency, elasticity and 'tolerance'.
The 6 speed gearbox for the
90 bhp 1.4 16v
Enhanced acoustic comfort, reduced engagement effort even
when cold and more precise gear engagement. These are the
advantages that the motorist can expect from the C514
gearbox (transverse configuration with two cascade shafts
and differential) on which various improvements were made to
the gear train, synchronisers, lubrication, internal gear
control and clutch control, before being used on the Fiat
Bravo.
The gearbox is available with six speeds for the 90 bhp 1.4
petrol engine, and adopts a gear control which prevents the
involuntary engagement of reverse, thanks to a stroke
limiter in the selector, and guarantees more precise
engagement of fifth and sixth. With this configuration, the
gearbox can transmit up to 128 Nm (13 kgm) at 4500 rpm. The
technical characteristics worth highlighting include the
gearing housing and clutch housing, both of which have been
optimised to reduce weight and to absorb more noise, using
FEM (Finite Element Method) calculation techniques. But also
Borg-Warner free-ring synchronisation on all speeds. And
finally, for first and second, the speeds most used by any
motorist, dual cone synchronisers have been fitted,
requiring 40% less engagement effort than the conventional
single-cone type.
The internal gear control system offers four levels of
selection, with a central positioner fitted with bearings.
Lubrication is dynamic, and the oil flows are channelled
through bore holes in the boxes. The advantages include
reduced wear, more efficient torque transmission and better
manoeuvring at low temperatures.
The 5-speed gearbox for the
120 bhp 1.9 Multijet (6 speeds for the 150 bhp)
This gearbox is available for the two 1.9 Multijet engines
(with 5 speeds for the 120 bhp version and 6 speeds for the
150 bhp version). It stands out for its configuration – 'two
shafts in a cascade with a differential', and for its
excellent manoeuvring and quiet operation. Synchronisation
of all forward speeds is of the Borg-Warner free-ring type,
and even reverse is synchronised. What is more, on first and
second, the synchroniser is of the triple cone type, while
the synchroniser on third, fourth, fifth and sixth is of the
single-tone type. The gearshift incorporates a syringe
device on the lever knob that prevents involuntary
engagement of reverse, and the gear control is activated by
a double Bowden metal cable system with an anti-noise
device.
Peak torque of 255 Nm (26 kgm) is already available at 2000
rpm on the 120 bhp 1.9 Multijet version, and 305 Nm (31 kgm)
on the 150 bhp 1.9 Multijet engine. And finally, clutch
control is hydraulic, incorporated into the gearbox with a
CSC device so that it requires less effort to activate,
while lubrication is dynamic, guaranteeing less wear, and
highly efficient torque transmission and manoeuvrability
even at low temperatures.
Suspension that guarantees
excellent handling and comfort
One of the goals set by the designers who developed the
Bravo was to create a suspension system that would offer
performance comparable with that of a higher class of car.
Devices that guaranteed easy, pinpoint steering, excellent
roadholding and the best comfort possible for passengers.
The choice went to two systems that emerged from a project
by Magneti Marelli and had already been used on other Fiat
models, suitably modified and updated.
Compared to the system adopted on the previous segment C
Fiat model, a total review of the geometries brought the
following changes:
- Tracks widened by 20 mm and larger tyres (in addition to
the consolidated 205/55R16, the Bravo is now available with
225/45 tyres on 17” wheels, and 225/40 tyres on 18” wheels)
- Modified suspension geometry, adoption of a new front
anti-roll bar and a new tuning of the springs and shock
absorbers suitable for the new bodyshell, with the best
torsional rigidity in the segment, new oversized
right-angled lower links designed to separate the effect of
the braking loads from the cornering loads to guarantee the
best balance in all driving conditions. In addition to
which, in spite of the wider track, the front geometry
design combined with the stroke of the steering boxes also
made it possible to contain the car’s turning circle: 10.5 m
between kerbs and 11 m between walls (values that are the
best in the segment).
- Rear suspension with interconnected semi-independent
wheels and a torsion axle created with a new stiffer
anti-roll bar to increase structural rigidity and to
maintain good suspension flexibility under load, thanks to a
reinforced hydraulic bushing to connect the rear axle to the
bodyshell. The suspension design also resulted in new
springs, dampers and buffers, in order to adapt to the
bodyshell and to improve the dynamic response on corners.
- Particular attention went into the design of the
components that could affect comfort in the car, adopting
solutions typical of higher segment cars, such as a
'dual-path' strut mount at the front and a vertical shock
absorber at the rear. These measures made it possible to
limit the effect of the vibration generated by the road
surface, without altering the structural rigidity or
detracting from steering precision.
- To increase stability on corners, the new car adopts
dampers with a 22 mm shaft on the Multijet versions (20 mm
on the 1.4 petrol engined versions) and a stiffened
reinforced hollow bar that also reduces the weight.
- Increase in the structural rigidity of the front
suspension anchorage crossbeam to improve acoustic and
vibrational comfort and to improve handling.
- And finally, the track of the front and rear suspension
was widened, both to adapt it to the larger exterior
measurements of the new model and to improve driving
stability.
Front
The Fiat Bravo adopts an independent layout in which the
shock absorbers and springs act as both damping and elastic
elements and as structural and kinematic elements. The main
components of this layout are the twin-shell wishbones made
of pressed sheet metal and not cast iron, which means a
significant weight reduction. The new model also introduces
some extremely interesting solutions:
- Front suspension crossbeam with great structural rigidity,
with a transverse connecting 'strap' close to the front
strut attachments.
- 'Dual-path' strut blocks to improve filtering of road
vibration, while guaranteeing excellent structural rigidity,
and enhancing steering precision.
- Stiffened anti-roll bar to limit vehicle rolling, with
shock absorber anchorage rods which boost the stabilising
efficiency and improve the promptness of the dynamic
response when cornering.
- New stiffer coil springs made with the 'side-load'
technique that optimise the thrust axis so as to reduce the
tangential forces on the damper shaft and therefore the
internal friction (system hysteresis), which improves
absorption of minor road roughness.
- To raise lateral rigidity and improve handling on corners,
the new model fits dual-rate telescopic dampers with a shaft
diameter of 22 mm on the Multijet versions and of 20 mm on
versions with the 1.4 petrol engine.
- And finally, bodyshell stiffening has been increased and
the upper anchorage to the bodyshell has been redesigned,
increasing the rigidity and the caster angle, which in turn
enhances steering precision and comfort.
Rear
The Fiat Bravo fits an optimised semi-independent system
with interconnected wheels and a torsion axle. The new
hollow anti-roll bar has been made 40% stiffer in order to
achieve a 40% anti-roll stabilising effect, improving
steering precision and roadholding. The soundproofing of the
vertical dampers, which are attached to the bodyshell in the
wheelarches, has been improved, to filter road roughness
better, enhancing acoustic comfort in the passenger
compartment.
And finally, the structure of the rear axle comprises
lateral arms pressed in two semi-shells, which are welded to
a lateral torsion profile, and the new anti-roll bar that
passes inside the crossbeam and is welded to the struts. The
rear axle attachment bushings are hydraulic to guarantee
better longitudinal absorption and comfort than the
rubber-metal type, with improved shoulders and
reinforcement.
The quality of life on board
Motorists have come to expect not only an enjoyable drive
but also well-being on board from any Fiat model. This means
surrounding the driver and passengers with technologies that
guarantee the highest levels of acoustic and climatic
comfort. The result is a muted, enveloping interior
environment, free from vibration thanks to the car’s
excellent soundproofing and the high torsional and flexural
rigidity of the bodyshell. There is more: the Fiat Bravo
proposes new versions of the Blue&Me™ system and CONNECT Nav
Plus, both developed by Magneti Marelli; dual-zone automatic
climate control, two audio systems (Hi-Fi and Hi-Fi Sound
System); comfortable, functional seats; and a large opening
sunroof. It is clear that the model fears no rivals where
comfort is concerned. And the Bravo offers the best
equipment available in the field of automatic systems that
reduce driving stress, like Cruise Control, a rain sensor
and a parking sensor. And last but not least, the new model
offers a tyre pressure sensor and numerous other features
that make travelling in the Bravo an extremely comfortable
experience.
NVH
(Noise-Vibration-Harshness) comfort
The Fiat Bravo has achieved an outstanding level of comfort,
which translates into quiet driving and an absence of
vibration. Quietness on a car is expressed by the
articulation index, which is an excellent 66% on the new
model, at a speed of 120 km/h. This has been made possible
both by the usual soundproofing packages and by the
extensive use of expansible diaphragms (positioned inside
the boxed elements to prevent noise from propagating inside,
and to isolate the passenger compartment from the outside
world). Vibration has been contained by building an
extremely rigid bodyshell structure. In terms of flexural
rigidity, an excellent value of 960 daN/mm has been
achieved, while torsional rigidity is 121,800 daNm/rad.
Particular attention was also addressed to the local
attachment rigidity of all the mechanical organs and the
suspension, which was designed to achieve the best possible
result in terms of handling and comfort on the road, in all
driving conditions.
Climate control
The climate inside the car is one of the main factors of
comfort during a journey, and it is also important for
preventive safety, because temperature, humidity and
ventilation affect the driver’s well-being and therefore his
attention level. Nor can we forget that the heating and
ventilation system is also responsible for demisting the
windscreen and side windows. The new model offers a choice
of three climate systems: a conventional heater, a manual
climate unit and an automatic dual-zone climate system. The
latter incorporates a control unit that automatically
controls the temperature, air flow, air distribution, and
activation of the compressor and the recirculation function.
The system also adopts an 'equivalent temperature' climate
control strategy. A number of sensors measure the indoor and
outdoor temperatures, and assess the sensation of thermal
well-being perceived by the passenger, i.e. the energy
exchange between the human body and the passenger
compartment, which is influenced by the humidity,
temperature and treated air flow. Another sensor, positioned
centrally at the base of the windscreen, measures the solar
radiation in the vehicle and the slope with which the rays
hit the passenger compartment. This makes it possible to
envisage any excessive increase in temperature inside the
car caused by the rays of the sun, and to predispose the
climate unit in time. The dual-zone system also allows
occupants to set two different temperatures and air flows,
on the left and the right sides of the passenger
compartment.
Panoramic sunroof
Life on board the Fiat Bravo is made more enjoyable by a
large sunroof (approximately 1.24 sq m, or 77% of the total
surface). It is made of two glass panels, a fixed panel at
the rear, and a front panel that opens electrically, and two
sunshades inside that slide towards the rear of the car. The
panoramic sunroof modifies occupants’ relationship with the
surrounding environment, letting them enjoy all the
luminosity and sense of freedom provided by the large glazed
surface. To give more light to the interior, it is possible
to open the sunshade and leave the window itself closed. To
travel in the 'open air', it takes a flick of the switch and
just seven seconds to open the front glazed panel and the
sunshade, and enjoy a 'window onto the sky'.
The radio and Hi-Fi system
The audio system on the new model is particularly
interesting, with the option of two radios and two audio
systems (Hi-Fi and Hi-Fi Sound System). The systems share
the same painstaking attention to the specifications and
distribution of the speakers (which feature Water Resistano
technology), designed and calibrated for the passenger
compartment. The first system, with a power output of 40 W,
includes two tweeters positioned close to the door handles,
two woofers in the front doors and two full range in the
rear side panels. The second level Hi-Fi Sound System has
the same equipment, plus two additional tweeters and a
subwoofer (260 W bass-reflex amplification) in the luggage
compartment, which creates a warmer, more enjoyable sound.
There is a choice of two radios (with a CD player or a CD
and MP3 file player) which are incorporated ergonomically
into the design of the dashboard. They are positioned in the
upper part of the facia (the best position for the driver)
where they are easily reached by the passenger, but can also
be managed by the controls on the steering wheel. Both units
have a Polished Black trim and grey keys, and include RDS
(Radio Data System), TA (traffic news), and PTY functions
(the code with which radio stations indicate the type of
music they broadcast, allowing the radio to automatically
select only the type of music preferred by the listener).
Every time the radio is turned on, it restores the settings
in place when it was turned off, while another device
automatically corrects equalisation on the basis of the
vehicle speed.
The customer can also choose between the 'pre-set equalised
effects', or carry out and memorise a personal setting of
the sound parameters. A 10-CD changer is also available from
Lineaccessori, which fits into the luggage compartment and
is managed by the radio controls.
Blue&Me™: communicating and
travelling without borders
One year after its launch, the Blue&Me™ system is enjoying
huge commercial success: it is requested by 20% of
purchasers of Fiat Auto models. That is not all. The
sophisticated device has also received a number of
prestigious international awards:
- from 'Frost & Sullivan', the 'Excellence in Technology of
the Year Award for European Automotive Telematics and
Infotainment market' (January 19, 2006);
- 'Telematic Update of Detroit' awarded it the prize for the
best telematic solution of the year (May 23, 2006);
- 'Automotive News Europe' awarded the 'Eurostats 2006'
prize to Giuseppe Bonollo, Vice President Product Portfolio
Management, for the success of the system installed in Fiat
Group cars (August 22, 2006).
Today, to mark the debut of the Fiat Bravo, Blue&Me™ takes
another step forward, offering the new Blue&Me™ Nav version.
In addition to the version marketed until now (hands-free
with Bluetooth® interface and advanced voice recognition –
USB port, MP3 player and SMS text interpreter), the new Fiat
model will offer a new version that incorporates the
convenience of a navigator, at an extremely competitive
price. In future, Blue&Me Nav will also activate additional
telematic services such as SOS and Concierge, and insurance
services.
Blue&Me™ Nav offers a simple, intuitive pictogram navigation
system that features an innovative method of introducing the
destination using voice controls. The destination is located
in real time: the map of the country is memorised on the USB
pen drive, and this makes access to the data faster and
quieter than when a CD is used. And with Blue&Me™ Nav, all
the functions are built in, and the telephone, music and
navigation information is available on the instrument panel.
What is more, as he navigates, the driver can listen to his
favourite music, which he has memorised, together with the
map, on the same USB pen drive or media player, or make a
telephone call using the hands-free device.
All the strong points of
the system
Blue&Me™ was developed in 3 years by Fiat Auto and
Microsoft. The partnership was ratified in June 2004, with
the long-term goal of designing innovative telematic systems
for cars, and it has created a product that has established
itself on the market, exploiting perfectly integrated
technology that is in complete harmony with the user, as its
name implies.
Based on the Windows Mobile for Automotive system, this
device features an open system that is always in step with
the times, updateable, flexible and modular. With the help
of Magneti Marelli, Fiat Auto and Microsoft offer a platform
that adapts to most cell phones, music players and other
personal devices, replacing current expensive, rigid
hardware, with the great benefit of being able to constantly
adapt to innovations on the market, remaining perfectly
integrated into the car. All at an accessible price.
Blue&Me™ is extremely safe and easy to use. The voice
control system, which is perfectly integrated into the
controls on the steering wheel and the information on the
instrument panel, allows a customer with a Bluetooth® cell
phone to use it even if the phone is in a jacket or bag,
without taking his hands off the wheel. And the advanced
voice recognition system allows immediate interaction,
because the voice does not have to be 'learned', even
allowing incoming text messages to be interpreted aloud.
Occupants can listen to hours and hours of digital music in
MP3, WMA and WAV format recorded on an iPod, a cell phone,
an MP3 player or a USB pen drive, by connecting a digital
device to the USB port, which is in an obvious position on
the centre console of the Fiat Bravo. The customer who
purchases the Blue&Me™ Nav system will receive a navigation
kit comprising a USB pen drive with the memorised map, and a
back-up CD that can be used to transfer the map onto a
personal MP3 player or iPod. The Nav key positioned on the
special board on the ceiling, connects directly to the
navigation menu, which can also be accessed via the controls
on the steering wheel, or vocally. The USB key is inserted
to start navigating, and the driver uses the keys on the
steering wheel to choose his destination by selecting the
initial letters of the address; he can even complete it
vocally.
Like all other information, the navigation details can be
displayed on the control panel: destination address,
pictograms of the directions to follow, information on
arrival and the usual vocal suggestions of the manoeuvres to
make, reproduced through the speakers. Unlike other
navigators, on which it is not possible to navigate and
listen to music CDs at the same time without a CD changer,
with Blue&Me™ Nav it is easy to navigate and listen to the
music saved in the media player. The navigation program can
be used on a personal computer together with the back-up CD,
to save the maps of a number of countries, purchased
separately, on the USB pen drive. Then the driver can select
a whole country (for example Italy, France, Germany, etc.),
or part of a country (for example northern/central/southern
Italy), or even a region that groups together maps of
different countries (for example northern Italy and
Switzerland, Austria and southern Germany).
CONNECT Nav Plus
On request the Fiat Bravo can be fitted with the CONNECT Nav
Plus system, a sophisticated, latest generation
infotelematic system that incorporates a satellite
navigator, radio, CD player, GSM dual-band hands-free
telephone, voice controls and the infomobility services.
Positioned at the centre of the facia, this device has a
6.5” 256-colour TFT active matrix screen, where the driver
can follow the indications regarding the route. CONNECT was
designed to put technology at the service of the driver and
to make life on board even more comfortable and easier
during the journey to one’s destination: the driver only has
to press the green key to access the GPS/GSM network and the
advantages of satellite communications, dialoguing aloud
with an operator, a personal assistant who is ready to
respond to any request for information, in the driver’s
language.
The various services available include:
- receiving information about traffic conditions on the
Italian motorway and superhighway network in real time,
customised to a particular route or area of interest;
- requesting the address or telephone number of a private
individual or company, from the Drive Me service. The
operator will send the information to the instrument display
panel by text message, after which the destination may be
selected by touching a single key, and it is equally simple
and immediate to call the number in the message without
having to key it in;
- a 24-hour online medical consultancy service.
Cruise Control
The Cruise Control system available on the Fiat Bravo helps
the motorist to control the vehicle speed, enhancing
travelling comfort. The device acts directly on the engine
throttle, automatically maintaining the cruising speed set
by the driver. It is only necessary to turn the ring on the
special lever positioned to the left of the steering wheel
to the 'ON' position, adjusting the speed using 'plus' (or
'minus'). When the ring is released the car will continue to
travel at the memorised speed without the driver having to
touch the accelerator pedal.
Cruise Control can function over the engine’s entire rpm
range, but only at speeds above 40 km/h. So it is advisable
to activate it in road conditions that will make it possible
to maintain the memorised value safely. If the accelerator
pedal is pressed (for example to overtake), Cruise Control
is momentarily over-ridden, but the system remains active.
The car will therefore accelerate as requested, but as soon
as the pedal is released, the system will resume the
memorised speed. For obvious safety reasons, the device is
automatically de-activated if the driver puts his foot on
the brake or clutch pedal. In this case, the 'RESUME' button
on the end of the Cruise Control system control lever must
be pressed to recover the pre-set speed.
To definitively de-activate Cruise Control and cancel any
previous setting, the ring nut must be turned to the 'OFF'
position and the engine turned off. A telltale on the
multifunction display indicates whether the system is
operating or de-activated. The ASR system (Anti Slip
Regulation) takes priority over the automatic speed control;
if ASR has to intervene, the system will then resume the set
speed.
Parking sensor
During parking manoeuvres, obstacles behind the car may be
outside the driver’s field of vision, or he may simply not
know how much space separates his car from the car parked
behind. In this situation the parking sensor can help; it is
activated every time reverse is engaged when the ignition
key is in the MAR position. The system comprises an
electronic control unit with an interface for the CAN
network, four ultrasonic sensors in the rear bumper and a
beeper. The four sensors cover both the rear side areas of
the car (from a distance of less than 60 centimetres), and
central rear area (from a distance of less than 150 cm).
We can see how it functions in detail. The four ultrasonic
transducers act as intelligent transmitters and receivers of
impulses. The latter are emitted every time reverse is
engaged; if they meet an obstacle they are reflected and
received like an echo by the sensor itself. At this point
the incoming signal is converted into a digital signal and
sent to the electronic control unit, which activates the
acoustic alarm. The information is then transmitted to the
driver by intermittent beeps, which become more insistent
until the car reaches a distance of 30 centimetres from the
obstacle, when the signal becomes constant.
The beeping stops if the lateral sensors detect an
approaching obstacle for more than three seconds, so that
the system does not continue to beep while parking along a
wall parallel to the vehicle axis. The parking system is
also available with eight sensors (the additional four
sensors cover the front end of the Bravo).
Rain sensor
Good visibility at all times is an important aspect of
preventive safety. Which is why the Fiat Bravo offers a rain
sensor, to ensure that the windscreen is always clean, even
in bad weather. The system is applied in the upper part of
the passenger compartment, behind the central rearview
mirror, and it automatically activates the windscreen wipers
and regulates their frequency depending on the intensity of
the rain. It is activated by moving the right-hand steering
wheel stalk to the first position (intermittency), and its
operation is based on the principle of the refraction of
infrared rays through the glass and the drops of water. The
optical element of the sensor (lens) sends an infrared ray
to the windscreen, which reflects it and sends it back to
the sensor. Because the luminous energy sent to the
windscreen is constant, the value measured on the light
received decreases as the quantity of water and other
impurities on the windscreen increases. The variation in the
signal is processed by the electronic element of the sensor,
which activates the appropriate wiper stroke frequency.
Since the wet surface disturbs the human eye more at night
than during the day, the sensor also regulates the wiper
strokes on the basis of ambient light. And it recognises
water streaks caused by worn blades, compensating for the
effects of the ageing of the windscreen and electronics. And
in particular situations, it activates special stroke
cycles: for example, when there are only a few drops of
rain, or impurities (saline deposits, dirt, etc.), on the
windscreen surface.
The sensitivity of the rain sensor can be modified by
adjusting the two-position ring nut on the right steering
wheel stalk. If the engine is stopped with the system
engaged, this is automatically de-activated. When the engine
starts again, the system can be re-activated by moving the
stalk to zero and then back to the first position, or by
adjusting the sensitivity of the sensor. To indicate that it
has been re-activated, the system will perform one stroke of
the wipers, even if the windscreen is dry. After the
windscreen washer pump has been used, the sensor is
activated automatically for the time necessary to catch the
drops dripping down the glass.
Tyre pressure sensor
The new Fiat model also includes a tyre pressure sensor, a
device that indicates any anomalies with both an acoustic
alarm and an icon on the display. The TPMS (Tyre Pressure
Monitoring System) monitors two conditions: insufficient
pressure and a puncture. If one of these two thresholds is
passed, the telltale will light up and a message will appear
on the display. And in the case of a puncture, the
instrument panel will also emit an acoustic signal.
'Small' devices for
outstanding comfort
The Fiat Bravo changes the quality of the way we live and
travel in a car. Thanks, for example, to the 'follow me
home' system that keeps the headlights on for a moment when
you get out of the car, or the new FIX&GO system to repair
punctured tyres, or tinted windows for greater privacy. The
customer can also choose electric rear windows with an
anti-pinch device built into the upper seal of the windows.
This device detects the presence of an obstacle between the
seal and the upper edge of the glass and immediately inverts
the direction of the window mechanism.
One of the most interesting features proposed on the new
model is the dead-lock, a technical solution that puts the
inside door handle and all the levers connected with the
lock, into neutral. This is an important step forward that
protects the car against theft: the dead-lock renders
ineffective any tool used by thieves to force the door or
its internal mechanisms. The device must be activated
deliberately (so that no one is locked in the car by
mistake). After the first turn of the key in one of the
front doors, or the first impulse of the remote control, a
second turn, or a second impulse, is necessary to engage the
car's dead-lock.
The Bravo also offers a cargo box which raises the loading
floor, making it possible to store small personal items in
the space below, and it also creates a single loading floor,
level with the folded seat. And finally, the entire range is
available with the Dualdrive power steering system which is
fitted with two functioning logics and uses the power
generated by a small electric motor instead of that supplied
by a hydraulic pump driven directly by the engine. What is
more, with the electric power steering system, the steering
response is correlated to the speed of the car: the higher
this is, the lower the level of servo assist and the more
effort required to steer, which guarantees more precise
steering. That is not all. This innovative electrical power
steering device offers customers another opportunity: that
of choosing between two different calibration programs. The
first, which enhances the understanding between the driver
and the car, is ideal on mixed out-of-town routes. The
second, which lightens the steering and therefore requires
less effort, is perfect in town and for parking manoeuvres.
The latter is engaged by pressing the 'city' key at the
centre of the facia. But if a driver takes to the motorway
and forgets to de-activate the device, it is not a problem.
To guarantee maximum safety at all times, above 30 km/h the
two systems provide the same amount of servo assist, thus
ensuring that the steering wheel responds correctly even at
high speeds.
The Piedimonte S. Germano
plant
The plant in Piedimonte S. Germano (Frosinone), where the
Bravo is built, is a centre of excellence among the world’s
automotive production plants. In 1972, Fiat chose the site
to install a state-of-the-art manufacturing facility. Since
its early years, the plant has played an important role: it
was here that the Robot-gate system was introduced for the
first time, before going on to become the benchmark for
automation in car manufacturing plants all over the world.
Here Fiat decided to invest to support the Bravo in
technological and qualitative terms, by developing an
innovative manufacturing model for the new car, based on a
balanced mix of advanced automation and human intervention
to control the quality that underpins the technology of the
new model. Today the Piedimonte S. Germano plant is on the
cutting edge of the world’s car manufacturing facilities.
There are no other plants in Europe that can boast a similar
technological or organisational level, in terms of the
manufacturing process and techniques.
The plant is in central Italy, and it is also in a central
position with respect to the other Fiat Auto manufacturing
facilities. It stands in an area of 2,033,072 square metres.
The facilities include a press shop, a panelling area,
painting and assembly, and much of the site is occupied by
Fiat Auto suppliers, which are thus fully integrated in the
manufacturing process and ready to intervene directly in the
various stages. About 3500 Fiat Auto employees currently
work in the plant, with an average age of 45 years. Working
hours are organised in two daily eight-hour shifts, five
days a week. Since it opened in 1972, the plant has turned
out numerous important Fiat models (in 2004 it celebrated
car no. 6,000,000 manufactured there), and production today
includes the Bravo, the Croma and the Stilo Multi Wagon.
Annual capacity is of over 250,000 cars, with a daily
capacity of about 1000 cars.
The plant has evolved constantly, and the manufacturing has
evolved from conventional systems to the robot-gate, the
high-automation plant and now the new manufacturing model,
known as the 'integrated modular plant' which represents the
most advanced structure in world car production.
In 2001, the manufacturing process at the plant was
completely re-designed, for an investment of almost Euro 400
million, and this required over one thousand days of
training for personnel at the plant. The transformation that
took place was based on the interaction of several factors:
- complete re-engineering of the manufacturing process;
- re-design of the line from the viewpoint of greater
ergonomics;
- a new organisation of activities on the line;
- the digital ETU (Elementary Technology Unit), developed
thanks to widespread computerisation throughout the
manufacturing process.
These four elements of change played a decisive role in
improving the capacity of the manufacturing process, which
translates into greater precision and better product
quality.
The re-engineering of the
manufacturing process and innovation for quality
The re-engineering of manufacturing optimised the quality
and efficiency of work on the assembly line. It focused on
the panelling and assembly areas in particular, although the
reorganisation regarded the whole process, and every single
stage in the process was made more efficient. A great deal
of attention was dedicated to quality checks: along the
whole process, each Bravo undergoes over 200 checks, most of
which are electronic.
1) Panelling. This is
an area of crucial importance for the quality of every car,
where advanced automation is decisive to determine the
quality of the product. The technological level is evident
from the figures: 437 spot welding robots, 18 continuous
seam welding robots, 916 welding calipers, a total of 280
actions. With the start of manufacture of the Bravo, several
new innovations were introduced in this area, including 2
new side tacking and finishing lines, 6 new robotised
islands to produce mobile parts (front and rear side doors,
bonnets), and five quality areas and three training areas
were set up. We should also point out that in 2004 about 100
new welding and handling robots from the NH4, H4, M1, S2 and
X1-500 family were introduced, to join the existing number.
They are fitted with electric motors and electric welding
calipers which give a hotter, cleaner and therefore better
spot weld. The panelling shop also includes two second
generation opto-electronic laser checking stations, for the
chassis and for the bodyshell. Both adopt the 'single tool'
system and work on-line. The double check guarantees the
perfect geometry of the car’s skeleton: the check on the
chassis, which precedes that on the bodyshell, is important
as it guarantees the quality of a part which will
incorporate the engineering, so that the precision of the
shapes and measurements is essential to ensure excellent
agility, driveability and roadholding.
To this we must add the innovation of the 'single tool'
system, which is a Fiat Auto exclusive, and verifies the
geometries of the chassis and bodyshell separate from the
carrier that transports them, so that a possible error in
the geometry of the support will not influence the laser
measurement. This solution is a real element of excellence
for the manufacturing system of the new model, because it
minimises the possibility of an error in the laser reading.
The 'Open gate' system has replaced the earlier
'Robot-gate', guaranteeing more precise preparation and
assembly of the sides, and more precise welding, because the
mechanical arms of the robots have more freedom of movement
inside the bodyshell. The 'Open gate' systems are specific
for each Fiat model.
The sealing of the spot welds is verified by a system of
ultrasound sensors; the sensor tests the weld and on the
basis of the amplitude of the response spectrum, may or may
not certify the quality of the weld. And finally, new
equipment included two new laser welding stations (side
doors), two robots to measure the doorway and to bore the
starting points for assembly of the vehicle front, plus a
robotised station to perform on-line measurements of the
panelled bodyshell (opto-electronic system).
2) Assembly. The
innovation introduced in the manufacturing process of the
Fiat Bravo was also significant at the assembly stage. First
of all, the bodyshell conveyor system was re-engineered, and
self-propelled units were introduced in the assembly
process, eliminating the unpleasant background noise and
achieving optimal comfort in the working environment.
Control units were introduced in the bodywork shop, with new
generation electro-air lifting, which improves the coupling
of the mechanical parts to the bodyshell.
And finally, on the new model, the glue is prepared and
spread on the windows by a latest generation robotised
system. And to prevent order-picking mistakes, the windows
are chosen on a computer using a multifunction display. The
actual bonding on the bodyshell is entrusted to the tactile
sensitivity of a worker who guarantees the correct position
of the glass at any point of the process.
3) Painting. The
paint shop was overhauled to introduce the 9 special colours
for the Bravo. A new Painting building was also constructed,
linked by a tunnel to the existing plant, which will employ
water-based paints that respect the new legislative
constraints. And finally, two new lines were built to use
water-based enamel, as well as a touch-up circuit and a
control unit for the paints. |
|